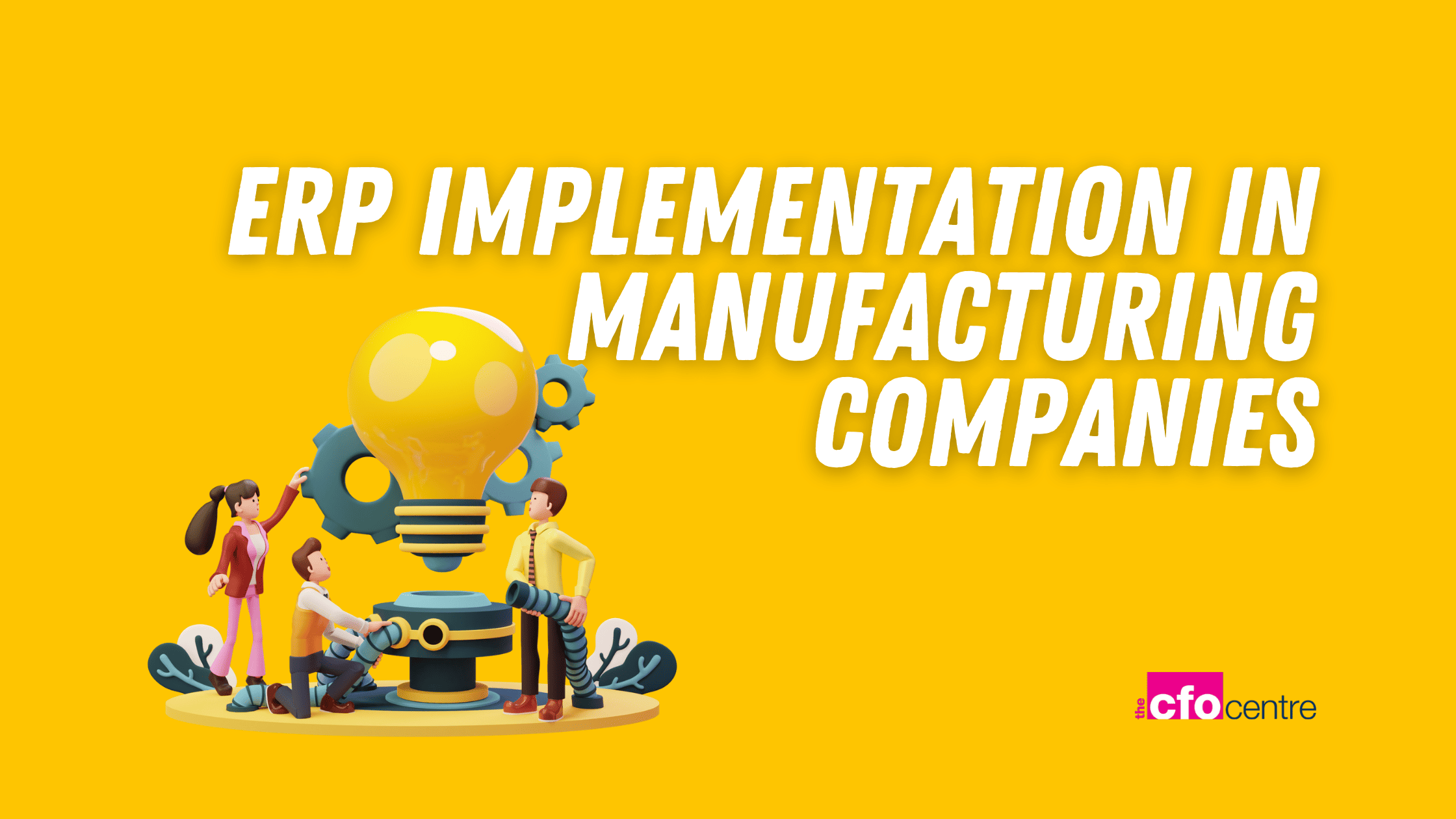
With data and data analysis gaining increased importance in decision-making, control, compliance, and reporting, it is imperative to prioritise good ERP to support business growth and profits.
ERP (Enterprise Resource Planning) is the integration of multiple functions across a business to maximise efficiency and productivity.
All 4 M’s – Machinery, Men (and women), Materials and Money are adequately addressed and administered in a good ERP.
ERP implementation in manufacturing revolves around 5 key areas:
- Quote-to-Cash (QTC) cycle –
The QTC process starts with a sales order and ends when payment is received for products sold. This is mainly applicable in Sales.
- Procure-to-Pay (P2P) cycle –
The P2P cycle concerns logistics and operations. The process starts when the business places an order for a service/good to an external vendor and ends when the vendors have been paid for services extracted.
- RM to FG (Production) cycle –
Managing the entire production cycle, starting at RM (Raw Materials) to FG (Finished Goods). This includes recording the bill of material and tracking the movement of inventory.
- HRIMS and Payroll Processing
- Record to Report cycle –
This mainly includes finance, accounts, and non-operational expenses like Marketing, Administration, Legal, etc.
The basic requirements for “proper” ERP Implementation
- Customer Master
- Vendor Master
- Inventory Master
- Chart of Accounts
The stronger the master, the better and faster the implementation. More importantly, stronger masters facilitate better reporting and improved long-term efficiency.
Benefits of good ERP Implementation
- Weekly flash reports on Orders, Sales, and Collections
- Monthly Profit & Loss Accounts, including comparisons with past performance and the budget.
- Monthly status of DSO (Days’ Sales Outstanding) of Accounts Receivable and DOS (Days of Supply) of Inventory.
- Slow moving/non-moving inventory analysis
- Product-wise margins and Invoice-wise margins
- Compliance reports for TDS and GST.
- Reports to expedite auditing in the desired format.
- Automated emails to place orders for raw materials, etc., and expedited collection – reduced labour hours.
- Better internal control by creating a Hierarchy of Approvals.
A company with proper ERP implementation will have access to an abundance of well-organised data. With the available data, they can create various desired reports to gauge the company’s performance and how best they can address all the stakeholders (owners, employees, customers, vendors, bankers, and government) in the organisation.
Hire a superstar part-time CFO
To help you increase cash, profit and valuation and free you up from the burden of day-to-day operations.